Electric gate repair involves diagnosing and fixing issues with automatic gates. Common problems include malfunctioning motors, damaged sensors, and broken hinges.
Electric gates provide security and convenience, but they can experience technical issues. Regular maintenance ensures their functionality and longevity. Common repairs involve addressing motor failures, sensor malfunctions, and physical damage. Professionals can quickly diagnose and fix these problems, restoring the gate’s performance.
Timely repairs prevent further damage and costly replacements. Proper care and routine checks extend the gate’s lifespan. Skilled technicians use specialized tools and knowledge to handle various gate types and brands. Ensuring your electric gate operates smoothly enhances security and convenience for your property. Always consult experienced professionals for reliable and efficient electric gate repair services.
Common Electric Gate Problems
Electric gates are a convenient and secure way to protect your property. But like any mechanical system, they can encounter problems. Understanding common electric gate issues helps you address them quickly. Below are some frequent problems and their possible causes.
Gate Not Opening Or Closing
One common issue is the gate not opening or closing properly. Several factors could contribute to this problem, including:
- Power Supply Issues: Check if the gate is receiving power. Inspect the circuit breaker and fuse box.
- Obstructions: Make sure nothing is blocking the gate’s path. Even small objects can prevent the gate from moving.
- Motor Malfunctions: The motor might be worn out or damaged. Listen for unusual sounds coming from the motor.
- Weather Conditions: Extreme weather can affect the gate’s operation. Snow, ice, or even heavy rain can cause issues.
If you notice any of these problems, it’s best to contact a professional for repairs. Ignoring the issue can lead to more significant damage over time.
Gate Making Strange Noises
Unusual noises coming from your electric gate can indicate a problem. Common sounds include grinding, squeaking, or clicking. These noises can be caused by:
- Worn Out Parts: Components like hinges, rollers, or the motor can wear out over time. Inspect these parts for signs of wear and tear.
- Lack of Lubrication: Moving parts need lubrication to function smoothly. Apply a suitable lubricant to hinges and rollers.
- Loose Components: Check if any parts are loose. Tighten screws and bolts as needed.
- Debris: Dirt and debris can get stuck in the gate’s mechanism. Clean the gate regularly to prevent this.
Addressing these issues promptly can prevent further damage and ensure your gate operates smoothly. Regular maintenance is key to avoiding noise-related problems.
Gate Not Responding To Remote
If your gate isn’t responding to the remote control, there could be several reasons:
- Dead Batteries: The simplest cause is dead batteries in the remote. Replace them and see if the issue resolves.
- Signal Interference: Other electronic devices can interfere with the remote’s signal. Move closer to the gate and try again.
- Remote Not Synced: The remote might have lost its connection with the gate. Refer to the manual to resync it.
- Receiver Issues: The gate’s receiver could be faulty. Inspect it for any visible damage.
Start with the easiest fixes, like changing the batteries. If those don’t work, more advanced troubleshooting or professional help might be needed.
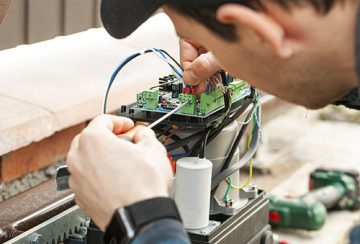
Credit: a1gateguys.com
Causes Of Electric Gate Problems
Electric gates provide convenience and security for homes and businesses. But like any piece of machinery, they can experience problems. Understanding the causes of electric gate problems can help you address issues quickly and efficiently. Below are some common causes of electric gate problems.
Power Supply Issues
One of the most common causes of electric gate problems is power supply issues. Without a reliable power source, your gate won’t function properly. Here are some common power-related issues:
- Power outages: A sudden loss of electricity can stop your gate from operating.
- Faulty wiring: Damaged or old wires can interrupt the power flow to the gate.
- Tripped circuit breakers: This can cut off the power supply to your gate motor.
To diagnose power supply issues, consider the following steps:
- Check if other electrical devices are working.
- Inspect the gate’s power cable for any visible damage.
- Reset the circuit breaker or replace any blown fuses.
Regular maintenance can help prevent power supply issues. Keep an eye on the wiring and ensure all connections are secure. Installing a backup power source like a battery can also be beneficial.
Sensor Malfunction
Sensor malfunctions can also cause electric gate problems. Sensors are critical for the smooth operation of your gate. They detect obstacles and ensure the gate opens and closes correctly. Common sensor issues include:
- Misaligned sensors: If the sensors are not aligned, the gate may not operate correctly.
- Dirty sensors: Dust or debris can block the sensors, causing malfunctions.
- Faulty sensors: Sensors can wear out over time and may need replacing.
To troubleshoot sensor problems, follow these steps:
- Check the alignment of the sensors and adjust if necessary.
- Clean the sensors with a soft cloth to remove any dirt or debris.
- Test the sensors by placing an object in their path to see if they detect it.
Regular cleaning and inspection of sensors can prevent many issues. Ensure they are correctly aligned and replace them if they show signs of wear and tear.
Worn-out Parts
Another common cause of electric gate problems is worn-out parts. Over time, parts of the gate can wear out due to constant use. Key parts that may need attention include:
- Gate hinges: These can become loose or rusty, affecting the gate’s movement.
- Gate motor: The motor can wear out, leading to slow or jerky movements.
- Control boards: These can malfunction, causing erratic gate behavior.
To identify worn-out parts, inspect the gate regularly. Look for signs of rust, wear, or damage. If you find any issues, replace the parts promptly to avoid further problems.
Consider these steps for maintaining your gate:
- Lubricate the hinges and moving parts regularly.
- Check the motor for unusual noises or slow operation.
- Inspect the control board for any signs of damage.
Regular maintenance can extend the life of your gate’s parts. Address any wear and tear quickly to ensure your gate remains in good working condition.
Diy Electric Gate Repair
Electric gates are a fantastic addition to any home, providing security and convenience. But they require maintenance and occasional repairs. DIY electric gate repair can save you money and time. With a few tools and some basic knowledge, you can fix many common issues. Let’s explore some simple steps to get your electric gate working again.
Checking Power Supply
First, ensure that your electric gate is receiving power. A power issue is often the easiest problem to fix. Follow these steps to check the power supply:
- Inspect the power source: Verify that the gate is plugged in or connected to a power source.
- Check the circuit breaker: Ensure that the circuit breaker hasn’t tripped. Reset it if necessary.
- Examine the wiring: Look for any frayed or disconnected wires. Replace or reconnect them as needed.
If everything looks fine, use a multimeter to test the voltage at the gate’s motor. The reading should match the gate’s specifications. If it doesn’t, there could be a problem with the electrical supply. Here’s a simple table to help you troubleshoot:
Voltage Reading | Possible Issue |
---|---|
0V | No power supply, check connections. |
Low Voltage | Potential power supply issue, check the source. |
Correct Voltage | Power supply is fine, check other components. |
Testing Sensors
Sensors are crucial for the proper functioning of your electric gate. They detect obstacles and ensure the gate opens and closes safely. To test the sensors, follow these steps:
- Clean the sensors: Dirt and debris can block the sensors. Wipe them clean with a soft cloth.
- Check alignment: Ensure that the sensors are aligned correctly. Misaligned sensors can cause the gate to malfunction.
- Test the sensors: Use an object to block the sensor path. The gate should stop or reverse direction.
If the gate does not respond, use a multimeter to check the sensor’s voltage. Here’s a quick guide:
Sensor Status | Action |
---|---|
No Response | Check wiring and connections. |
Incorrect Response | Re-align or replace the sensors. |
Normal Response | Sensors are functioning well. |
Replacing Worn-out Parts
Electric gates have many moving parts that can wear out over time. Replacing these parts is essential for maintaining the gate. Here are the common parts you might need to replace:
- Rollers: Worn-out rollers can cause the gate to stick. Replace them if they look damaged.
- Hinges: Check the hinges for rust or wear. Replace if necessary.
- Drive belt: Inspect the drive belt for cracks or wear. Replace it if needed.
To replace these parts, follow the manufacturer’s instructions. Make sure you have the right tools and replacement parts. Here’s a table to guide you:
Part | Signs of Wear | Replacement Steps |
---|---|---|
Rollers | Sticking, noise | Remove old rollers, install new ones. |
Hinges | Rust, looseness | Remove old hinges, install new ones. |
Drive Belt | Cracks, slipping | Remove old belt, install new one. |
Regular maintenance and timely repairs can extend the life of your electric gate. Always consult your gate’s manual for specific instructions. Keep your gate in top shape to enjoy its benefits for years to come.

Credit: pssgaragedoorsandgates.com
When To Call A Professional
Electric gates offer convenience and security for homeowners. But like any mechanical device, they can break down. Knowing when to call a professional for electric gate repair can save you time, money, and ensure your gate operates smoothly. Here are some key instances when professional help is necessary.
Complex Gate Problems
Electric gates can develop issues that are too complex for the average homeowner to handle. These problems often require specialized knowledge and tools. Here are some scenarios:
- Electrical malfunctions: If your gate isn’t responding, it could be an electrical issue. Diagnosing and fixing electrical components requires expertise.
- Motor issues: The motor is the heart of your gate. If it’s not working, the gate won’t move. Repairing or replacing a motor is a job for a professional.
- Sensor problems: Sensors ensure your gate opens and closes safely. If they malfunction, the gate might not operate correctly. A professional can recalibrate or replace them.
Attempting to fix these complex problems without the right knowledge can lead to further damage. A professional ensures the job is done right the first time.
Lack Of Repair Experience
Repairing an electric gate requires specific skills and experience. If you lack this experience, you might face several challenges:
- Incorrect repairs: Without experience, you might fix one problem but create another. Professionals know how to diagnose and repair without causing additional issues.
- Prolonged downtime: Inexperienced repairs can take longer, leaving your gate out of commission. Professionals can quickly identify and fix the problem, minimizing downtime.
- Costly mistakes: Mistakes during DIY repairs can lead to expensive fixes. Professionals help avoid these costly errors.
Hiring a professional with the right experience ensures your gate is repaired quickly and correctly, saving you time and money in the long run.
Safety Concerns
Electric gates are large, heavy, and powered by electricity, which poses safety risks. Here are some safety concerns that warrant calling a professional:
- Electric shock risk: Working with electrical components can be dangerous. Professionals have the training to handle these safely.
- Injury risk: Gates are heavy and can cause injuries if they malfunction. Professionals know how to handle and repair them safely.
- Security concerns: A malfunctioning gate can leave your property vulnerable. Quick, professional repairs ensure your gate remains secure.
Ensuring the safety of your family and property is paramount. Professionals have the expertise to address safety concerns effectively.
Choosing The Right Repair Service
Electric gates are a convenient way to secure your property and offer ease of access. Over time, these gates may need repairs. Choosing the right repair service is crucial to ensure your gate operates smoothly and safely. This guide will help you understand what to look for in a repair service.
Experience And Expertise
Experience and expertise are vital when selecting an electric gate repair service. An experienced technician can quickly diagnose and fix issues, saving you time and money. Look for repair services that have been in the business for several years.
Here are some key points to consider:
- Years in business: A service with many years of experience is likely more reliable.
- Certifications and training: Ensure the technicians are certified and have undergone proper training.
- Specialization: Some services may specialize in specific gate brands or types.
Consider asking the following questions:
- How long have you been repairing electric gates?
- What types of gates do you specialize in?
- Do your technicians have any certifications?
A table can help compare different services:
Service | Years of Experience | Specialization | Certifications |
---|---|---|---|
Service A | 10 | Residential Gates | Yes |
Service B | 5 | Commercial Gates | No |
Customer Reviews
Customer reviews provide insights into the reliability and quality of a repair service. Positive reviews indicate satisfied customers and trustworthy services. Check multiple platforms to get a well-rounded view.
Look for reviews that mention:
- Timeliness: Did the technician arrive on time?
- Quality of work: Was the repair effective and long-lasting?
- Customer service: Was the interaction friendly and professional?
Here are some ways to find reviews:
- Google Reviews: Often the most comprehensive source.
- Yelp: Another platform with detailed customer feedback.
- Social Media: Check the company’s Facebook or Instagram pages.
“The technician arrived on time and fixed our gate quickly. Excellent service and very professional. Highly recommend!”
Warranty And Pricing
Warranty and pricing are critical factors in choosing a repair service. A good warranty ensures the repair will last, while transparent pricing prevents unexpected costs.
Consider these aspects:
- Warranty length: Longer warranties indicate confidence in the work.
- What’s covered: Ensure the warranty covers parts and labor.
- Pricing transparency: Get a detailed quote before the repair starts.
- What is the length of your warranty?
- What does the warranty cover?
- Can I get a detailed quote?
Service | Warranty Length | Coverage | Pricing Transparency |
---|---|---|---|
Service A | 1 Year | Parts and Labor | Detailed Quote Provided |
Service B | 6 Months | Parts Only | Estimate Only |
Preventive Maintenance For Electric Gates
Electric gates add convenience and security to homes and businesses. Regular preventive maintenance for electric gates ensures they function smoothly and last longer. This blog post covers the essentials of keeping your electric gate in top condition.
Regular Cleaning
Regular cleaning is the first step in maintaining your electric gate. Dirt and debris can cause mechanical problems. Clean your gate at least once a month using mild soap and water. Avoid harsh chemicals as they can damage the gate’s finish.
Here are some tips for effective cleaning:
- Use a soft cloth or sponge to clean the gate.
- Rinse thoroughly to remove soap residue.
- Dry the gate with a clean towel to prevent rust.
- Check for cobwebs and remove them as they can interfere with the gate’s sensors.
If your gate has a painted finish, inspect it for chips or scratches. Touch up any damaged areas to prevent rust. Regular cleaning not only maintains the gate’s appearance but also ensures smooth operation.
Lubrication Of Moving Parts
Lubricating moving parts is crucial for the smooth operation of your electric gate. Over time, friction can cause wear and tear. Lubricate the gate’s hinges, rollers, and tracks every three to six months.
Follow these steps for proper lubrication:
- Clean the parts to remove dirt and old lubricant.
- Apply a high-quality lubricant specifically designed for gates.
- Wipe off excess lubricant to prevent dirt buildup.
- Operate the gate a few times to distribute the lubricant evenly.
Using the right lubricant is important. Avoid using grease or heavy oils as they attract dirt. Instead, use a silicone-based or lithium-based lubricant. Regular lubrication reduces friction and extends the lifespan of moving parts.
Professional Inspections
Professional inspections are essential for identifying potential issues before they become major problems. Schedule an inspection with a qualified technician at least once a year. They will check the gate’s electrical components, sensors, and mechanical parts.
A professional inspection typically includes:
Component | Inspection Task |
---|---|
Electrical System | Check wiring and connections for wear or damage. |
Sensors | Ensure sensors are aligned and functioning correctly. |
Mechanical Parts | Inspect hinges, rollers, and tracks for wear. |
Control Panel | Test the control panel for proper operation. |
Professional inspections help detect problems early, saving you from costly repairs. Keep a record of all inspections and maintenance tasks. This log helps track the gate’s condition and ensures timely upkeep.
Benefits Of Timely Electric Gate Repair
Electric gates offer convenience and security for homes and businesses. Timely electric gate repair ensures these benefits are maintained. Understanding the benefits of timely electric gate repair can help you make informed decisions about maintaining your gate.
Improved Security
Regular electric gate repairs enhance your property’s security. A well-maintained gate functions properly, preventing unauthorized access.
Key benefits include:
- Reliable operation: A functioning gate closes and locks securely.
- Enhanced deterrence: A robust gate deters potential intruders.
- Immediate response: Quick repairs address vulnerabilities promptly.
A broken gate can be a security risk. Prompt repairs eliminate weak points, ensuring your property remains safe. Regular inspections and maintenance keep your gate in top condition.
Install safety features like motion sensors and alarms. These additions improve your gate’s security. Keeping your gate in good repair ensures these features work effectively.
Increased Lifespan Of Gate
Timely repairs extend your electric gate’s lifespan. Regular maintenance prevents small issues from becoming big problems.
How timely repairs help:
- Prevent wear and tear: Addressing minor issues prevents major damage.
- Maintain components: Regularly serviced parts last longer.
- Improve performance: A well-maintained gate operates smoothly.
Ignoring minor problems can lead to costly replacements. Regular repairs ensure your gate’s components stay in good shape, saving you money in the long run.
Below is a table showing the benefits of timely repairs:
Timely Repair Benefit | Impact |
---|---|
Reduced wear and tear | Longer lifespan |
Maintained components | Fewer replacements |
Improved performance | Smoother operation |
Reduced Repair Costs
Fixing small issues early reduces overall repair costs. Timely electric gate repairs prevent expensive damage.
Benefits of reduced repair costs:
- Lower expenses: Small repairs cost less than major fixes.
- Avoid replacements: Regular maintenance prevents costly replacements.
- Budget-friendly: Predictable maintenance costs help with budgeting.
Emergency repairs can be costly. Regular inspections and timely fixes keep repair costs manageable. Planning for regular maintenance is more cost-effective.
Early detection of issues prevents larger problems. Addressing them quickly saves money and extends your gate’s life. This approach ensures your gate remains functional without breaking the bank.
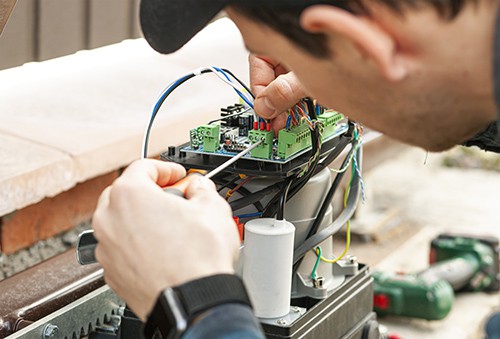
Credit: a1gateguys.com
Frequently Asked Questions
How Do You Troubleshoot An Electric Gate?
Check power supply first. Inspect remote batteries and functionality. Examine gate tracks for obstructions. Test motor and wiring connections. Consult the manual for specific troubleshooting steps.
How Do You Fix An Electric Gate That Won’t Close?
Check the power supply first. Examine the gate’s sensors for obstructions. Inspect the remote control batteries. Verify the gate motor for issues. Consult a professional if problems persist.
What Is The Life Expectancy Of An Electric Gate Motor?
The life expectancy of an electric gate motor ranges from 10 to 15 years. Regular maintenance can extend its lifespan. Quality and usage frequency also play a role.
Why Do Electric Gates Stop Working?
Electric gates may stop working due to power outages, motor issues, sensor problems, or obstructions in the track. Regular maintenance is essential.
Conclusion
Ensuring your electric gate is in top condition enhances security and convenience. Regular maintenance can prevent costly repairs. Trust professional services for reliable and efficient electric gate repair. Your safety and peace of mind are worth it. Invest in quality repairs to extend the life of your gate system.