Common safety hazard issues at the workplace include slips, trips, falls, and ergonomic injuries. Electrical hazards, chemical exposures, and fire risks are also prevalent.
Workplace safety is paramount for the well-being of employees and the smooth operation of any business. Identifying and addressing safety hazards is not only a legal requirement but a moral imperative to ensure workers go home healthy each day. Accidents such as slips and falls might seem trivial, yet they account for a significant number of workplace injuries yearly.
Repetitive strain and ergonomic injuries can arise from poor workstation design, affecting long-term employee health. Electrical hazards present immediate risks of shocks or fires, while chemical exposures can have both acute and chronic health impacts. Regular training, risk assessments, and safety protocols can mitigate such hazards, fostering a culture of safety that benefits both the organization and its staff. By maintaining vigilance and adopting best practices, workplaces can reduce accidents and maintain a high standard of safety.
Intro To Workplace Safety
Imagine a place where every task shines with safety. This place is the vision of an ideal workplace. An environment free from accidents and incidents is not just a goal but a necessity. Workplace safety is an umbrella of practices and protocols. These practices aim to keep workers from harm’s way.
Every industry bears its unique set of risks. Still, common safety hazards can occur anywhere. It’s essential to identify and mitigate these risks. Doing so ensures the well-being of employees and the smooth operation of businesses.
Why Safety In The Workplace Is Paramount
The importance of safety in the workforce cannot be overstated. A safe work environment promotes employee morale. It also contributes to productivity. Employers must foster a culture of safety. This culture minimizes risk and protects all involved. Everyone deserves a safe place to work.
- A decrease in accidents means fewer injuries. This leads to fewer days off work.
- Safety practices reduce legal liability for employers. They ensure compliance with laws.
- Training and safety equipment are investments. They show commitment to worker welfare.
Statistics And Impact Of Poor Safety Standards
Safety shortcomings have measurable impacts. Statistics paint a clear picture. The consequences of neglecting safety are significant. They affect individuals, businesses, and the economy.
Statistic | Impact |
---|---|
Number of Work-Related Injuries | Decreased productivity |
Costs from Accidents | The financial strain on businesses |
Average Days Lost to Injury | Loss of individual earnings |
Effective safety protocols are cost-saving. They preserve both health and profits. The value of a safe workplace is immense, transcending mere numbers.
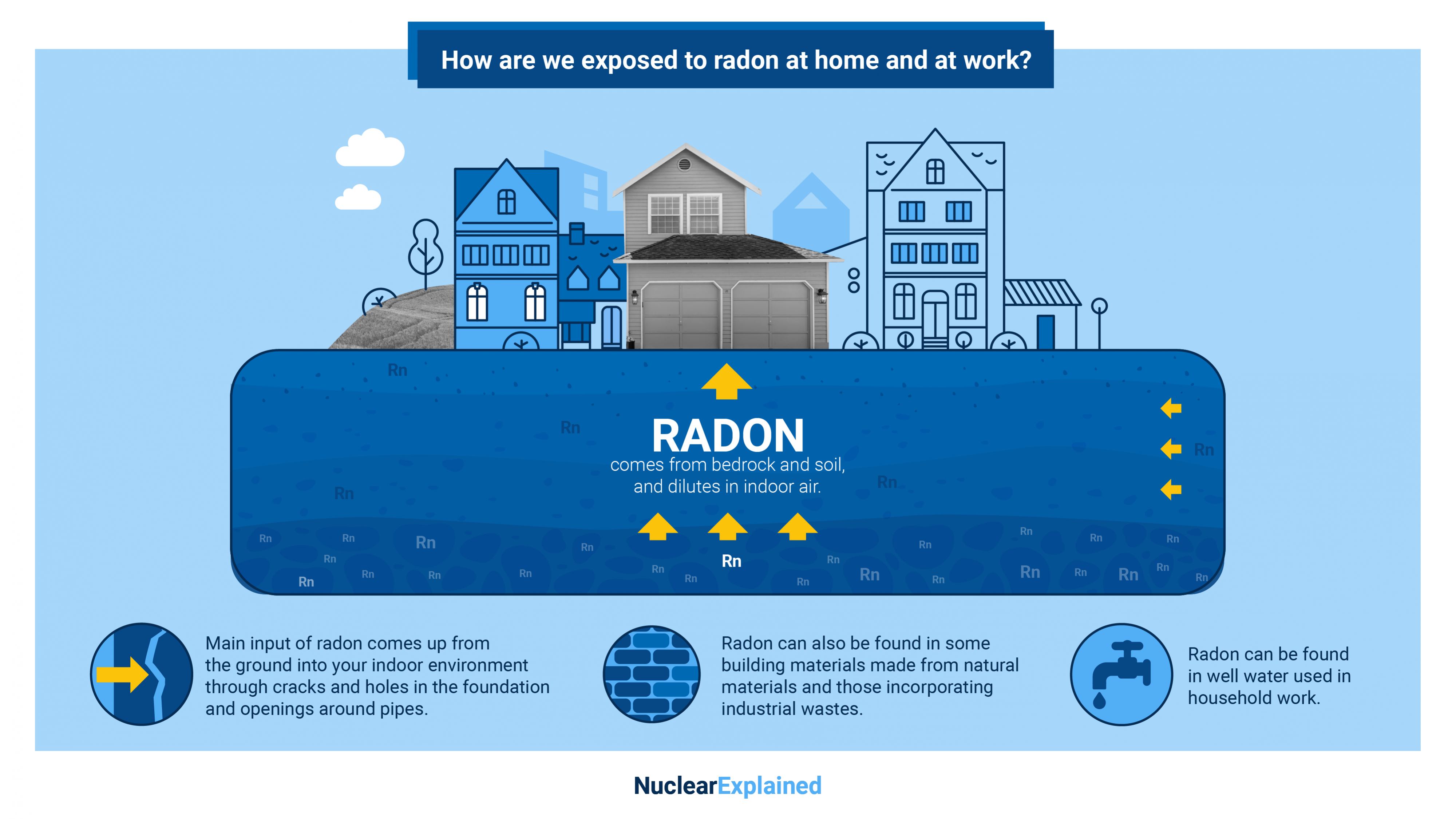
Credit: www.iaea.org
Slips, Trips, And Falls
Slips, trips, and falls are among the most frequent causes of workplace injuries. They can happen anywhere, from office hallways to construction sites. Every employee risks encountering these hazards. Understanding the causes and implementing effective prevention strategies is key to maintaining a safe work environment.
Causes And Prevention
Slips occur when there’s too little traction between footwear and the walking surface. Trips happen when an object blocks the path. Falls can result from slips and trips or from a misstep off an elevated area.
Common causes include:
- Wet or greasy floors
- Loose mats or rugs
- Clutter or cables in walkways
- Uneven walking surfaces
- Improper footwear
Prevention strategies:
- Maintain clean, dry floors
- Secure mats and rugs
- Organize cables and remove clutter
- Use signs for uneven floors
- Encourage proper footwear
The Role Of Proper Signage And Training
Clear signage is crucial for alerting employees to potential hazards. Warning signs must be visible. They inform about wet floors, uneven surfaces, or areas undergoing maintenance.
Regular safety training is critical. It equips staff with the knowledge to identify and avoid hazards. Role-playing exercises and drills ensure that they can apply this understanding.
Signage Type | Purpose | Location Example |
---|---|---|
Wet Floor | To warn of slippery conditions | Near restrooms or cleaning areas |
Uneven Surface | To alert of changes in floor level | In construction areas |
Construction Notice | To inform of ongoing work and associated risks | Around renovation sites |
Ergonomic Hazards
Ergonomic hazards lurk in most workplaces. They can lead to discomfort, injury, and reduced productivity. These hazards stem from poor workstations, repetitive tasks, and improper handling techniques.
Identifying Risky Work Practices
Spotting ergonomic risks calls for a keen eye. Look out for:
- Repeated motion
- Awkward postures
- Long periods without breaks
Workers performing the same task throughout the day or using forceful exertions are at higher risk. Regular breaks help prevent strain injuries. Observing daily routines reveals these risky practices.
Investing In Ergonomic Solutions
Workplaces can improve ergonomics by:
Strategy | Benefits |
---|---|
Adjustable furniture | Supports various body types |
Ergonomic tools | Reduces strain |
Proper training | Teaches correct usage |
Investing in adjustable chairs and desks allows workers to tailor their workstations. Ergonomic tools designed to minimize effort help reduce hand and wrist strain. Training ensures workers use equipment properly, further reducing injury risk.
Fire Safety Concerns
Keeping employees safe at work is a top priority. Among the various hazards, fire poses a significant threat to safety and business continuity. Understanding fire safety concerns in the workplace is essential. A mindful approach can prevent devastating losses and ensure a secure environment for all.
Common Causes Of Workplace Fires
Fires can occur anywhere and at any time. Let’s look at typical causes in the workplace:
- Electrical faults: Overloaded circuits and faulty wiring can spark a blaze.
- Combustible materials: Flammable liquids and gases can ignite easily.
- Equipment mishandling: Improper use of machinery can cause overheating or sparks.
- Human error: Accidental or negligent behaviors add risk.
- Arson: Intentional acts of setting fires pose catastrophic threats.
Fire Prevention And Response Planning
Being prepared is the best defense against a workplace fire. Here’s what businesses can do:
Prevention Strategies | Response Measures |
---|---|
Install and maintain smoke alarms and fire extinguishers. | Conduct regular fire drills to ensure everyone knows evacuation routes. |
Keep all areas free from clutter that could fuel a fire. | Train staff in using fire extinguishers and emergency equipment. |
Store flammable materials securely and safely. | Create an emergency plan that includes assembly points and headcounts. |
Perform regular inspections of electrical systems. | Have a communication plan for informing all stakeholders in the event of a fire. |
Every business needs a tailored fire prevention and response plan. It must address specific risks and comply with local fire safety regulations. Regular training and awareness campaigns can make a big difference in preventing workplace fires and saving lives.
Electrical And Wiring Hazards
Workplaces brim with various safety challenges, but electrical and wiring hazards stand out for their potential to instantly harm employees. From overloaded circuits to exposed wiring, these dangers can cause severe injury, fires, or even fatalities. Awareness and preventive measures are keys to a safe work environment.
Recognizing Unsafe Electrical Conditions
Unsafe electrical conditions can lurk unnoticed. Workers must be able to spot the telltale signs of potential danger. These include:
- Frayed wires or insulation cracks
- Electrical panels blocked or difficult to access
- Sparks from outlets when plugging in devices
- Oversized fuses or breakers that can cause fires
- Continual tripping of circuit breakers
- Use of extension leads as a permanent solution
Best Practices For Electrical Safety
Creating a safe workplace requires adherence to best practices in electrical safety. Here are effective strategies:
- Regular inspections of electrical equipment
- Clear access to all electrical control panels
- Use of adequate protective equipment (PPE)
- Training employees on emergency procedures
- Maintenance of equipment and replacing or repairing damaged parts
- Ensuring all electrical installations comply with national safety standards
Hazardous Substances And Chemical Risks
Workplaces often house hazardous substances and chemicals that can pose significant health risks. These can range from cleaning products to heavy-duty industrial chemicals. Without appropriate management, they can lead to accidents, health complications, and even fatalities. Understanding these risks is the first step towards creating a safer working environment.
Managing Chemical Storage And Use
Proper storage and use of chemicals are critical in minimizing workplace hazards. Employers must ensure that all chemicals are stored safely and according to regulatory standards. This involves:
- Labeling containers clearly with hazard information.
- Maintaining an up-to-date inventory of chemicals.
- Training employees on proper handling procedures.
- Implementing spill response protocols.
Separation of incompatible substances is also crucial to prevent dangerous reactions. For instance, acids and bases should be stored apart to avoid hazardous interactions.
Personal Protective Equipment (PPE) Requirement
Using personal protective equipment (PPE) is essential when handling chemicals. PPE acts as a barrier between the chemical and the worker, reducing exposure risks. The type of PPE required can vary but often includes:
Type of PPE | Use Case |
---|---|
Gloves | Protecting hands from burns and absorption. |
Goggles | Shielding eyes from splashes. |
Aprons | Protecting skin and clothing from spills. |
Respirators | Preventing inhalation of fumes. |
Each employee must be trained on how to use and maintain their PPE properly. Regular inspections ensure that PPE is in good condition and ready for use when necessary.
Machinery And Equipment Dangers
In any workplace, machinery, and equipment are vital tools. Yet, they pose significant risks if not managed properly. Understanding and mitigating these issues is essential for maintaining a safe environment.
Ensuring Regular Maintenance And Inspections
Machines require consistent care to function safely. Neglect can lead to unexpected malfunctions or failures. To prevent accidents, a routine maintenance schedule is crucial.
- Check machinery for signs of wear and damage.
- Replace parts that are broken or worn out.
- Ensure all safety guards are in place and secure.
Maintenance logs should be up-to-date and thorough. They serve as a record for inspections and repairs. This history helps track the machine’s performance over time.
Safety Training For Operators
Proper training is essential for anyone who operates machinery. This training should include:
Training Component | Description |
---|---|
Machine Operation | How to use the equipment safely and correctly. |
Emergency Procedures | Steps to take in case of a malfunction or accident. |
Risk Identification | Spotting potential hazards before they cause harm. |
Training must be ongoing to stay effective. Refreshers courses keep operators aware and prepared. Certifications can help ensure operators have the knowledge they need.

Credit: naspweb.com
Psychosocial Hazards At Work
Workplaces are not just about physical safety. Psychosocial hazards significantly affect employees’ well-being. These issues stem from workplace culture, social interactions, and the mental demands of the job. They may not always be visible but they can deeply impact morale, productivity, and mental health. Recognizing these hazards is crucial in creating a safe and supportive work environment.
Dealing With Stress And Work Pressure
Stress and work pressure sneak up silently but weigh heavily on employees. Identifying triggers is the first step to management. Employers can help by ensuring workload matches workers’ capabilities. Regular breaks and a supportive environment are key. Stress-management workshops can also equip staff with coping strategies.
- Identify stress triggers
- Match workload with capability
- Encourage regular breaks
- Provide stress-management resources
Preventing Bullying And Harassment
Bullying and harassment are toxic to any workplace. Preventing these behaviors starts with clear policies. Education plays a big role. Regular training sessions can highlight the impact of bullying. They also show how to report incidents. A strong support system for victims is essential.
Strategy | Details |
---|---|
Policy Development | Implement clear anti-bullying guidelines. |
Education | Conduct regular awareness training. |
Reporting | Create easy-to-use reporting channels. |
Support | Have a system to help affected individuals. |
Preventive Measures And Safety Protocols
Workplace safety is paramount in maintaining a productive environment. Recognizing potential hazards and implementing preventive measures can drastically reduce the risk of injury. Adherence to safety protocols ensures that both employees and employers are aware and prepared to handle unexpected situations effectively. Let’s explore some essential strategies to foster a safer workplace.
Conducting Risk Assessments
Risk assessments
are vital to identify hazards. Regular assessments lead to safer work practices. Here is a step-by-step approach:
- Spot potential hazards in the workplace.
- Decide who may be harmed and how.
- Evaluate risks and decide on precautions.
- Record findings and implement them.
- Review the assessment and update if necessary.
Conducting these assessments creates awareness and prevention pathways.
Creating An Effective Safety Culture
Building a safety culture is a team effort. Engage employees with these steps:
- Provide safety training to all staff members.
- Discuss safety often and make it a priority.
- Encourage the reporting of hazards without penalty.
Action | Impact |
---|---|
Regular Safety Meetings | Keeps safety at the forefront of daily operations |
Employee Training | Equips employees with knowledge to avoid injury |
Transparent Reporting Systems | Ensures issues are addressed promptly and effectively |
An inclusive approach to safety builds trust and promotes adherence to protocols.
Dealing With Accidents
Workplaces are bustling zones. Safety hazards can lurk everywhere. When accidents occur, knowing how to respond is critical. Speed and knowledge save lives and prevent further injuries. It’s important to have a solid plan for dealing with workplace accidents. This includes first aid and emergency response, followed by thorough investigation and learning. These steps maintain safety and ensure the well-being of all employees.
First Aid And Emergency Response
First aid stations prove crucial during emergencies. They must be accessible and well-stocked. Trained individuals should be ready to use them. Quick actions like these matter:
- Calling for help immediately.
- Using a first aid kit to manage minor injuries.
- Conducting CPR if necessary.
- Identifying escape routes in case of fires or disasters.
Regular first-aid training sessions prepare employees for emergencies. Emergency drills teach them how to act fast.
Investigation And Learning From Incidents
The post-accident investigation uncovers causes. It helps prevent future incidents. Companies should follow these steps:
- Gather facts about what happened.
- Analyze these facts to find the root cause.
- Develop strategies to avoid repetition.
Transparent communication plays a key role. Sharing findings increases awareness. It promotes a culture of continuous safety improvement. Educating staff on these findings helps them understand the importance of protocols. It makes the workplace safer for everyone involved.
Regulations And Compliance
Navigating the complex maze of workplace safety can often seem daunting. A safe workplace is not only essential for employee well-being but it is also mandated by law. Understanding regulations and ensuring compliance is pivotal to maintaining a risk-free work environment. In this regard, let’s delve into what it takes for businesses to stay on the right side of the law.
Understanding Your Legal Obligations
Every employer has a legal responsibility to ensure their workplace meets specific safety standards. These obligations are designed to prevent accidents and injuries on-site. Failure to comply can lead to serious legal consequences, including fines and legal action. It’s imperative to know what the law requires of your business.
- Assess risks regularly to keep the workplace safe.
- Provide adequate training and resources for employees.
- Maintain records of all safety measures and incidents.
Staying Up-to-date With Safety Standards
Safety standards can change as new risks emerge and technologies evolve. Staying informed about the latest safety protocols is crucial. This includes discipline in regularly reviewing policies and ensuring they align with current standards.
- Subscribe to safety newsletters and bulletins.
- Attend safety training sessions and workshops.
- Consult with safety professionals for expert advice.
Fostering Employee Engagement
Employee engagement is critical to promoting a safe workplace. Engaged employees are more aware of their surroundings. They follow safety protocols. They care about their well-being and that of their colleagues. To enhance safety in the workplace, companies must nurture this engagement. This can be done through various strategies.
Encouraging Safety Reporting And Suggestions
Creating an open channel for safe communication is vital. Employees should feel comfortable reporting hazards. They should suggest improvements without fear. A transparent safety reporting system encourages this behavior.
- Implement an anonymous reporting tool.
- Host regular safety meetings.
- Make feedback forms readily available.
Such measures make employees active safety participants. They help identify and mitigate risks promptly.
Rewarding Safe Behavior
Recognizing and rewarding safe behaviors reinforces their importance. It stimulates a culture of safety at the workplace. Employees feel appreciated. They remain motivated to adhere to safety standards.
Initiative | Description | Impact |
---|---|---|
Safety Milestone Rewards | Celebrate without incidents. | Encourages ongoing caution. |
Employee Safety Committees | Peers nominate safe employees. | Boosts peer recognition. |
Spot Awards | Immediate recognition for safe acts. | Instant positive reinforcement. |
Incentives can range from public acknowledgments to bonuses. Each acts as a strong motivation for keeping safety at the forefront.
Conclusion: Continuous Improvement In Safety
Staying safe at work isn’t a one-time task; it’s an ongoing commitment. To keep workers safe, businesses must always look for ways to improve. Whether it’s by setting new goals or embracing tech, safety is a journey, not a destination.
Benchmarking And Setting Safety Goals
Knowing where you stand is key to getting better. Comparing safety performance to industry standards helps pinpoint areas needing attention. Clear, achievable goals motivate teams and guide safety strategies. Here’s how to set the bar:
- Review past incidents and near-misses.
- Identify frequent hazards.
- Learn from industry leaders’ best practices.
- Set specific, measurable objectives for improvement.
Embracing Technology And Innovation For Safety
Tech advancements create smarter, safer workplaces. Tools like wearable monitors, mobile reporting apps, and automated safety checks cut risks dramatically. Innovation keeps workers informed and alert. See tech at work:
- Wearable devices track health in real-time.
- AR goggles provide safety training simulations.
- Apps streamline incident reports and response.
Remember, staying safe is about never standing still. By setting benchmarks and embracing new solutions, we can make the workplace secure for everyone.

Credit: naspweb.com
Frequently Asked Questions On Common Safety Hazard Issues At Workplace
What Are Typical Workplace Safety Hazards?
Workplace safety hazards can be categorized into physical, chemical, biological, ergonomic, and psychosocial risks. Common examples include slips, trips, falls, improper use of chemicals, poor ergonomics, and workplace stress. Identifying and addressing these is crucial for worker protection.
How Can Employers Prevent Accidents At Work?
Employers can prevent workplace accidents by conducting regular risk assessments, providing appropriate training, and maintaining equipment. Establishing clear safety protocols and encouraging a culture of safety also play significant roles in accident prevention.
What Safety Equipment Should Employees Use?
Employees should use safety equipment tailored to specific hazards they face. This often includes hard hats, safety goggles, gloves, earplugs, and proper footwear. Personal protective equipment (PPE) is vital for minimizing the risk of injury.
Can Workplace Design Reduce Safety Hazards?
Yes, workplace design can significantly reduce safety hazards. The incorporation of ergonomic furniture, adequate space for movement, non-slip flooring, and well-placed lighting can prevent many common workplace injuries. Design should always prioritize safety and functionality.
Conclusion
Ensuring a safe work environment is paramount for every organization. By recognizing and addressing common hazards, employers can significantly reduce accidents. Remember, a commitment to safety is a commitment to your team’s well-being and overall productivity. Foster a culture where hazard awareness is second nature, and watch as workplace safety rises to new heights.